Precise measurement using precipitation technology, Ruike Intelligent is committed to empowering automated testing of electronic components
Surface mount components are widely used in the manufacturing of various forms of electronic devices, and are gradually developing towards miniaturization and precision. In order to meet the needs of new technologies, the testing standards for electronic components such as capacitors and pins have also been correspondingly increased. Therefore, the appearance and functional testing of capacitors and pins have become particularly important.
To measure the excellence of electronic components, a series of tests and evaluations need to be conducted from multiple aspects. So, the accuracy and stability of the testing equipment are particularly important. Therefore, a machine vision that can replace the human eye to accurately locate, measure, detect, and make judgments is naturally very important.
At the same time, the requirements for component quality in the electronic industry are constantly increasing, and components are developing towards miniaturization and precision. In response to this challenge, electronic product manufacturers are constantly adjusting their industrial layout and production processes, strengthening the appearance inspection of internal components such as capacitors and pins during the production process, and preventing problems such as bulging, damage, and misalignment of products. Dongguan Ruike Intelligent Technology Co., Ltd. (hereinafter referred to as "Ruike") has achieved significant results in the visual inspection system for the aforementioned electronic industry.
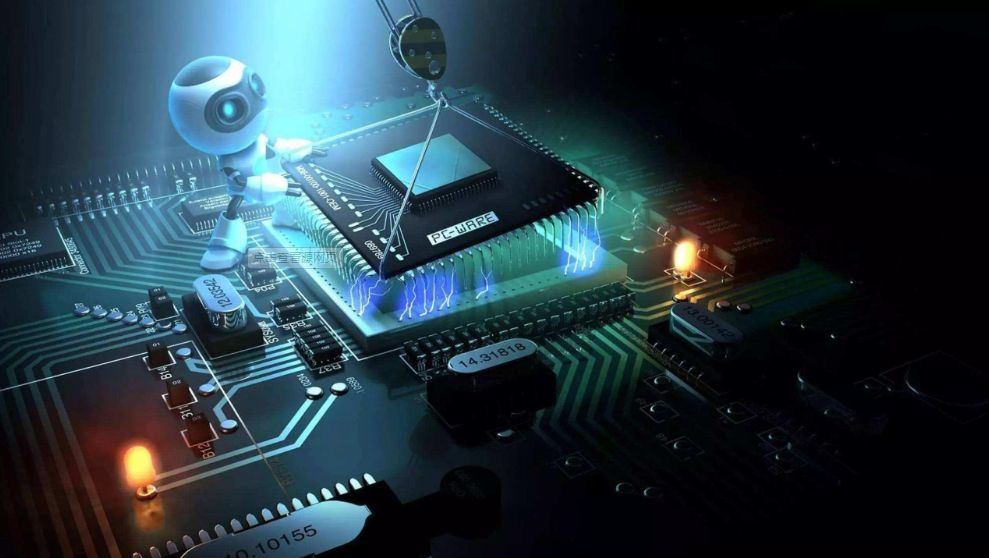
As a leader in the professional production of optical vision (non-contact) automated testing equipment in China, Ruike now has high-precision, high reliability, and cost-effective standard optical image screening equipment, such as glass discs, U-slots, indexing disc image screening machines, eddy current and 360 degree tooth injury detection equipment, and provides customized services and automated testing solutions, committed to improving efficiency in hardware, equipment manufacturing, plastic products, and other fields Productivity and quality.
In response to the high standards and requirements for capacitor quality in the electronics industry, in order to achieve full automation of the capacitor quality testing process, Ruike has successfully developed automated capacitor testing equipment. The glass disk detection equipment mainly detects whether the capacitor has bulges, upper and lower surfaces, and the size of the product; The indexing plate detection equipment mainly detects the appearance of capacitors, positive and negative electrodes, and the height of hidden lines, with a detection accuracy of ± 0.02mm and a detection speed of up to 200 per minute. The launch of automatic capacitance testing equipment has replaced manual repetitive testing work, enabling 100% automatic inspection of products, improving testing efficiency, ensuring the accuracy of the testing process, and enhancing customer competitiveness.
And the needle arrangement automation detection equipment can detect frame slot reverse material, needle hole damage, pin height, frame slot reverse material, needle hole damage, etc., with a detection speed range of 300-1200pcs/min, which can be scientifically adjusted according to the product. These automated testing equipment applied to electronic component testing greatly improve labor productivity, while helping customers reduce costs and increase efficiency, greatly improving product production efficiency and quality.
Over the years, in order to conduct in-depth research and development of intelligent and accurate automated testing equipment and understand market demand, Ruike has closely monitored the system integration of automation equipment in various industries and fields such as automotive fasteners, hardware manufacturing, and consumer electronics, collecting more frontline needs to help Ruike's equipment functions develop towards stronger, more precise, and more intelligent directions. At present, Ruike's automated testing equipment has been widely applied to component manufacturers and has received unanimous recognition from customers. For example, it has been applied to automated testing in the production process of capacitors, pins, gaskets, wire pressing frames, spring washer bolts, and other products. Some technical difficulties encountered during the testing process have also been overcome by Ruike's R&D team one by one.
It is precisely because of Ruike's continuous efforts in research and development innovation, deep cultivation of optical vision (non-contact) automated testing, after years of sedimentation, Ruike gradually emerged in the automation market and achieved remarkable results. It was awarded the certificate of "China Famous Brand" key promotion unit and the title of "Top Ten Equipment Brands" for Chinese fasteners in 2013, with excellent product quality High quality service and comprehensive solutions have won the trust of customers and are at the forefront of visual inspection technology in China.
来源声明:本文章系english编辑原创或采编整理,如需转载请注明来自english。以上内容部分(包含图片、文字)来源于网络,如有侵权,请及时与本站联系(400-8560-998)。